Inside Supply Management Magazine
Resiliency in Light of Brexit and Other Barriers
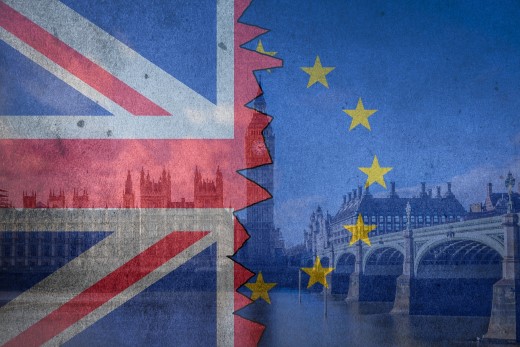
By Richard Wilding, OBE
Brexit is an obvious example of a threat and obstacle to supply chains — but it’s also part of a global trend towards more uncertainty, increased tensions and protectionist trading policies. Our expectation of a natural evolution towards ever-loosening markets and free-flowing goods is now looking like complacency.
There are the broken trade negotiations between U.S. and China, and a greater willingness to talk tough and introduce tit-for-tat tariffs is creeping into more international negotiations. In the Middle East, Qatar is under an economic embargo from its neighbors. Switzerland, currently going through its own renegotiations with the European Union (EU) on trade and financial services, is experiencing difficulties with movement of goods across the neighboring French border. Although perhaps unrelated, residents on or near the border have reportedly complained of a higher level of spot checks in enforcement of the 1 kilogram duty-free meat allowance.
It’s the kind of small but purposeful change that leaves a bitter taste and can prompt retaliation and an escalation of measures. The wrangling over how the top EU jobs — including president of the European Central Bank — should be shared across larger and smaller member states is another worrying sign of how the mood is changing.
Past Responses
The United Kingdom (U.K.), has been stuck in an extended period of limbo. An initial flurry of advice from government to businesses on the need for stockpiling to avoid shortages of essential materials has been followed by an edgy silence, suggesting that less certainty exists over whether there are any “right” or “wrong” answers on stockpiling.
Figures suggest U.K. manufacturers stockpiled raw materials in the first quarter of 2019 at the highest rate since the early 1990s. The supply management profession knows this is an issue: a recognized phenomenon (call it demand amplification, the Forrester effect or bullwhip effect) with long-term implications for supply chains and the U.K. economy as a whole. Warehouse space is in short supply, and the delay of Brexit to October 31 produces a Halloween trick for retailers: having to stockpile for Brexit, Christmas and Black Friday at the same time. This could be a treat for consumers due to potential discounting to clear stock.
Stockpiling as a response is nothing new; it was one of the U.K.’s biggest worries in 1999. If the so-called millennium or Y2K bug took down IT systems, U.K. supply chains were ready. Businesses generally looked at increasing their stocks by 12.5 percent, in case of emergency.
The U.K. Department of Trade and Industry asked our team at Cranfield School of Management to assuage business concerns and try to dissuade organizations from stockpiling. We investigated companies’ stockpiling plans and modeled what they would mean in practice. Based on a 12.5-percent planned increase in stocks, the sudden burden of “dead money” was clotting up operations: Finances invested in stock limited any ability to grow. Looking at the real accounts of organizations, a retailer’s growth prospects were reduced in this context by more than 1 percent, while the wholesaler and manufacturer were pushed into a minus-growth situation. Wasteful investment increased the chance of business failures.
Stockpiling Implications
Small variations in customer demand result in large variations in demand being transmitted up and down the supply chain. A cycle of over-ordering and stockpiling leads to demand distortion, and any further over-ordering contributes to the amplification. Typically, a demand increase of 12.5 percent will be passed to a supplier as an increase of 26 percent, resulting in that supplier placing an increased order for their own supplier of 55 percent — resulting in big oscillations in inventories and supplies that can occur for many years.
For the economy as a whole, there is the danger of boom and bust cycles until that distortion works its way out of the system. Meanwhile, the increased costs put more strain on smaller firms — at a time when more businesses choose larger supplier partners.
These kinds of lessons seem to have been lost — and we need to be careful about the implications. More communication between retailers, wholesalers and chains of manufacturers is needed, with parties (1) being honest about potential problems, (2) working to dispel mistrust about capacity and supplies and (3) discussing what “necessary” looks like, as well as what could be an overreaction.
The implications of stockpiling on organizational agility need to be accounted for in decision-making. Companies should be looking to negotiate with suppliers and customers now to develop strategies for holding stocks across the supply chain. This way, will it be possible to build confidence within supply chains — and make it easier to deal with any shocks that come.
Supply Chain Resilience
Regardless of the cause of the barriers and uncertainty— whether extreme weather or political turmoil — the same principles apply when it comes to building a resilient supply chain.
Consider the “temple” of supply chain resilience: As shown in the figure below, the foundation needs to be an effective supply chain strategy — this impacts the supply chain’s risk profile by defining the supply chain processes, infrastructure, information systems and supply chain organization (how people within the supply chain relate).
[caption id="attachment_21827" align="aligncenter" width="700"](Courtesy of Richard Wilding, OBE)
The floor of the temple is product design — as supply chain risk often occurs during a product’s design stage. For example, when considering what goes into a product and the sourcing of materials, risk might be avoided if different materials are used or if the product can be designed to be configured according to customer’s needs.
The pillars are:
●Internal and external collaboration, which leads to greater resilience
●Supply chain risk management culture, as practitioners should always ask how supply chain risk will be affected
●Supply chain design, which includes the locations, network and equipment used
●Agility, to ensure flexibility within the supply chain operations.
The temple roof is supply chain transparency. With high levels of transparency across product flows and networks, parties can be assured the supply chain is operating effectively through connected information systems and good communication. While simple paper-based supply chain maps are useful for making sure all members have a clear understanding of the supply chain, big data and predictive analytics can provide additional levels of transparency.
The crown is continuous monitoring and intelligence. It’s imperative to ensure that your employees, suppliers and customers keep you informed of issues, so you can act more quickly than your competitors.
Ensuring supply chain resilience is a critical element of any supply chain strategy, and by considering the temple approach, the impact of a disruptive event can be mitigated. Stockpiling is one approach organizations can use to mitigate risk, but it can be risky. Resilience that goes far beyond stockpiling of goods to creating agility and flexibility throughout the supply chain, enabling a response to any change in conditions — including in an unpredictable environment like Brexit — a supply management organization can always keep ahead, securing the resources it needs to keep its supply chain operational.
Richard Wilding, OBE, is professor of supply chain strategy at Cranfield School of Management at Cranfield University in Cranfield, England.