Inside Supply Management Magazine
Talent Issues Can Affect Equipment Maintenance
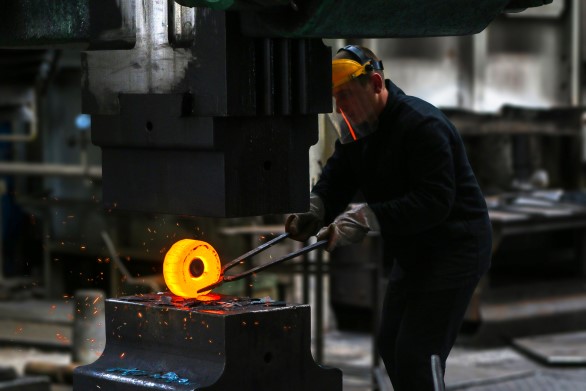
The manufacturing sector is facing numerous talent challenges that are leading to equipment maintenance issues. Suppliers — as well as their customers that rely on components and parts from those manufacturers — could ultimately be affected, says Jason Rowan, MBA, assistant vice president, lead engineering specialist at Johnston, Rhode Island-based FM Global, one of the world’s largest commercial property insurers.
There has been an uptick in the frequency of breakdowns in major equipment across a wide range of industries that rely on machinery and industrial systems, according to FM Global. A survey commissioned by the company of 200 business leaders found that the risk of equipment failure is a big concern. Three in four respondents expect it would take months for their companies to financially recover from the breakdown of critical equipment.
Talent factors contributing to the risk include:
A changing workforce. Manufacturing is competing for talent, “and a lot of people are choosing tech,” says Rowan, who is based in Norwood, Massachusetts. This talent shift, especially when combined with baby-boomer retirement, is resulting in a downsizing of the workforce, he says: “This is going to put further emphasis on OEMs, third parties and suppliers for equipment guidance, maintenance and parts. But it’s a double-edged sword — like the manufacturers, some third parties and suppliers are experiencing the same workforce reduction.”
An aging workforce. As technology advances, “it might be difficult for certain generations to adapt to new systems, feel a level of comfort with automated processes or perform any sort of diagnostics or prognostics that they were responsible for,” Rowan says.
Lack of knowledge transfer. As aging workers retire, they often take with them knowledge that could be useful to the younger generations stepping in. Training and mentoring can help, Rowan says. “Closing the gap on knowledge transfer will help reduce concerns associated with equipment failure,” he says. “That means that a company should have to have adequately trained and informed employees capable of assessing equipment failures, and in the case of failure, what must be done to get it back up and running.”
Other challenges include:
●Aging manufacturing infrastructure — as the infrastructure ages, equipment breakdown becomes more likely.
●Concerns about a potential recession or economic downturn. “If you have economic downturns, you’re going to have restrictions on capital-intensive budget projects and you’re going to be limited as to how much money can be invested in new or upgraded equipment,” Rowan says.
Fixing the talent issues will require a collaborative effort. “This isn’t going to be a change that’s overnight,” Rowan says. “It’s going to require organizations to realize that they have a real concern.” Since they may not be getting the support they need to fix the equipment, they may experience quality and timing issues, which potentially could result in negative reactions from customers, he says: “That ultimately could hurt their bottom line and their customers.”
Embarking on a three-step plan can help manufacturers manage operations issues:
1) Assessment. Companies need to accurately assess and forecast how they might be challenged during future operations, Rowan says. “Looking ahead at the age and experience of the technical personnel, the infrastructure life expectancy and outlook for industry demand will create more transparency for senior management to plan for the future.”
2) Succession plan. “This will allow you to properly manage knowledge transfer and address any gaps identified in the process,” Rowan says. “This translates to any training requirements that are needed, such as continuing education, coaching or mentoring needs, and any site- or equipment-specific guidance.”
Sometimes, employees need that equipment-specific guidance or hands-on experience that a computer program won’t each them, he says: “Computer-based programs are typically written for ideal scenarios; they’re not real world. Real-world scenarios are really taught on the job, and you have to be out there to experience them.”
3) Engagement. “The third point is to strategize and stay engaged — try to stay in touch with industry news and events and have a lessons-learned mindset that can help shape the internal strategy of the organization,” Rowan says. “This isn’t a static strategy; it’s very dynamic and allows for economic shifts, cultural changes, and anything in between.”