The China Supply Chain Conundrum
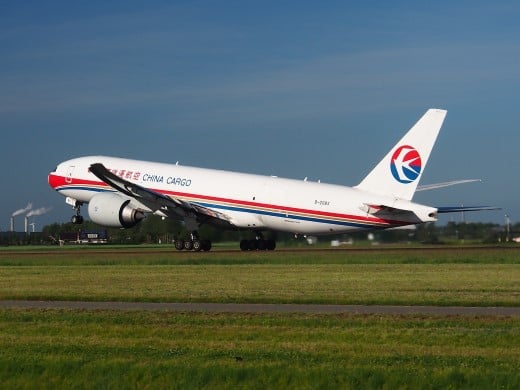
As the coronavirus (COVID-19) pandemic rages on in the U.S., chatter from Washington about loosening China’s grip on supply chains that serve American consumers, particularly in the health-care sector, is threatening to turn into a cacophony. However, while many companies have reduced their dependence on China — a process that began during the trade war — the rhetoric on completely restructuring supply chains is facing hard realities.
China’s manufacturing and supply chain advantages have been fostered over decades and are deeply entrenched, says Doug Guthrie, Ph.D., professor of global leadership and executive director of China initiatives at the Phoenix-based Thunderbird School of Global Management, an affiliate of Arizona State University. Guthrie’s research platform, On Global Leadership, has a three-person team in Shanghai, China, and its findings mirror research by Institute for Supply Management® (ISM®) that indicates COVID-19 is not hastening a supply chain exodus from China.
Results of a third round of coronavirus surveying, conducted in May by ISM Research & Analytics, are covered in the July/August issue of Inside Supply Management®. From the article: Fifty-seven percent of respondents’ companies are not considering reshoring or nearshoring, while 15 percent are planning to move operations, and 6 percent have done so. Also, respondents indicated their companies’ average manufacturing capacity in China is 76 percent, up from 53 percent in Round 2, while average U.S. capacity dropped, to 74 percent from 79 percent. “We are more dependent on China, as its recovery is faster,” wrote one respondent, a supply manager at a transportation equipment manufacturer.
“There’s a lot of misunderstanding of just how powerful China is in its supply chain development, infrastructure and management, and many companies just can’t afford an alternative,” Guthrie says. “And for some big technology companies, it’s impossible. Even if a smaller company could (go elsewhere), if it’s spent the last 10 years cultivating relationships and building a supply chain in China, probably wants to see a return on that investment.”
He adds, “It’s just not the case that the trade war or coronavirus is causing companies to pack up and leave China. I know that frustrates a lot of politicians in the U.S., but the dynamics are not that simple.”
China’s Enduring Supply Chain Might
Beijing boasts a triple crown of supply chain assets — the country’s massive (270 million people) mobile manufacturing labor population, vocational- and technical-trained workforce and unmatched infrastructure. Guthrie says he has advised companies that did not set out to establish manufacturing and sourcing operations in China, but executives determined that the country, due to its level of vocation and technical training, had the most advanced workforce.
Thanks in big part to the Made in China 2025 policy, which is designed to encourage production of high-value technology products and services, “a lot of innovation is driving a manufacturing transformation in China,” Guthrie says. Also, the nation has become the world’s biggest consumer market, as well as the fastest growing.
A departure of some lower-value manufacturing during the trade war has impacted the country, as many companies determined that, tariffs or not, they were overextended there. Employing a “China plus others” mindset, organizations have diversified operations, but that doesn’t necessarily reduce their risk, explains James Gellert, CEO of RapidRatings, the New York-based software-as-a-service (SaaS) technology firm.
“They removed their Tier-1 problem, but the companies’ new Tier 1 (suppliers) are still relying on Chinese companies for their Tier 1s,” Gellert says. “So, you haven’t necessarily reduced your risk; you’ve just pushed it further and deeper into your supply chain and taken lower-tier risk that you wanted to avoid. You’ve onboarded a new supplier, but you really haven’t fully managed the risk. In some cases, you may have compounded it.”
Changing Procurement Hearts and Minds
China’s technology manufacturing and supply chain might was no secret, but the COVID-19 crisis exposed how dependent the U.S. was on other countries for medical supplies. That dynamic has been emphasized by recent flooding that has devastated Wuhan, China, the epicenter of the coronavirus pandemic, and nearby Xiantao, home to the country’s largest manufacturer of fabrics for personal protective equipment (PPE).
Before the pandemic, China was exporting more PPE, N95 masks, surgical masks and medical goggles than the rest of the world combined, according to research by the Washington, D.C-based Peterson Institute for International Economics. The level of America’s reliance on China (or any other country) for active pharmaceutical ingredients is unknown, as that data is not tracked by the U.S. Food and Drug Administration.
Nancy LeMaster, MBA, is Chair of ISM’s Hospital Business Survey Committee that will generate data for the Hospital PMI™, a third index in the ISM® Report On Business® that debuts on August 7. She says the health-care sector became so dependent on supplies from countries like China, Puerto Rico and India by overemphasizing costs — which will be a hard habit to break. She cites the IV fluid shortages after Hurricanes Maria and Irma hit Puerto Rico in 2017: Companies did not move production to the U.S. in part because health-care systems balked at making long-term volume commitments at potentially higher prices.
“That’s where it gets sticky,” LeMaster says. “People say they want to change and (move production), but not if it costs more. … So, I’m a little skeptical. I hope we’ll find ways to collaborate with suppliers to have more transparency and diversification, but it will take a big change for that to happen.”
Focusing on a ‘Fundamental’
Several wild cards — including a possible second global coronavirus wave, as well as U.S. elections in November and potential subsequent trade-policy changes — could impact companies’ manufacturing and sourcing in China. However, Beijing is unlikely to relinquish its status as a supply chain behemoth.
In the era of trade turbulence, Chinese muscle-flexing and a global pandemic, Gellert says, strong supplier relationships and effective risk management are among an organization’s most valuable assets.
“There is and should be circumspect diligence around suppliers in China and in other markets that were most dramatically affected (by COVID-19),” he says. “That doesn’t mean everyone should stop working with companies in those markets. But they need to understand the risks and manage them.
“The idea that we’ll never work again with a company in China doesn’t make any sense. But the idea that we should better understand companies that we’re working with makes a lot of sense. … That’s just fundamental.”