A Proactive Design for Boosting Supply Chain Performance
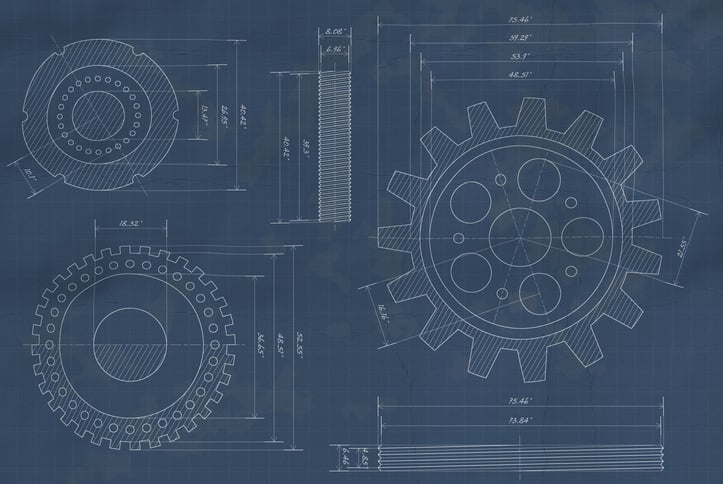
The coronavirus pandemic has caused the concept of supply chain design to evolve — and interest in it to accelerate.
Once considered a model of network optimization based on landed costs, supply chain design has become a digital approach that enables companies to optimize resilience, agility, cost and service, says Nathanael Powrie, executive vice president and digital practice leader at Boston-based supply chain and operations consulting firm Maine Pointe.
Contributing to the changes are “the volatility in the market, rapid change in customer buying habits, and uncertainty of supply are making traditional supply chains obsolete,” he says. “It’s been difficult for companies to keep pace and meet the needs of their diverse customer base even without disruptions like global pandemics.”
Additionally, companies are bombarded with more data than ever, yet many have legacy systems that “are highly fragmented when it comes to being able to have a holistic view of their supply chain performance and insights,” Powrie says. Such systems aren’t designed for fast and smart decision-making — a must in today’s world — and, he says, “don't have an end-to-end data reference model that incorporates data from, for example, planning, inventory management and sales.”
Legacy systems also make it difficult for executive stakeholders to understand business rules and metrics and don’t have the capability to pull in advance analytics with rich visualizations. “These barriers have to be removed when you're developing a model for supply chain design,” Powrie says. “If you don't have access to what your business rules are in the physical workplace, how are you going to recreate that in a digital space?”
As a result, many companies are still using spreadsheets for strategic planning, he says: “With that, there’s not an effective way for them to evaluate scenarios and trade-offs.”
Defining Supply Chain Design
Under supply chain design, Powrie says, a set of capabilities and tools are used to optimize supply chain resiliency and agility while improving cost and service. “It's a way to determine the actions that business they should be taking for the biggest impact and how they get ahead of potential issues,” he says. “And, regarding external and internal changes, how have they adapted and evolved?”
Supply chain design is the practice of building supply chain modeling to understand where assets or nodes should be located and how they can be rationalized to meet targeted service levels, Powrie says. An example of a targeted service level could be implementing two-day delivery capabilities. “It's all about understanding the costs and constraints of your existing network,” he says, “and evaluating the capacity can unlock the abilities for companies to determine the long-term strategy.”
A company can use the tools to look at manufacturing footprints, labor conditions and transportation trade-offs, among other areas, to become more strategic, he says. While the tools involve complex mathematical modeling, next-gen cloud-based platforms, have evolved to a point where users with no data science and advanced analytics backgrounds can still use them, he says.
That accessibility has been a game-changer, he says, noting that in the past, accessibility was once a barrier to implementation. The latest supply chain modeling tools are programmed with the ability to automate what-if scenarios, he says, thus allowing for enhanced decision-making.
The Supply Chain Digital Twin
By using a digital twin — essentially a virtual representation of the physical supply chain — a company can run what-if scenarios. “From there, companies can use the data from the digital twin to optimize the physical workspace,” Powrie says.
Such an exercise shouldn’t be an isolated scenario but should become part of a company’s business plan or sales and operations planning program, he says. Benefits to continuing digital what-if scenarios include the ability to improve service levels and thus customer satisfaction. “On-time, in-full is still a huge hot button for CEOs,” Powrie says. “If they were able to switch carriers or switch lanes, what would that do to those service levels?”
Another benefit: reduced costs, sometimes as much as 10 percent or 15 percent, due to such factors as improving inventory conditions, more strategic sourcing and enhancing relationships, he says.
“This is really about optimizing their supply chain with the ability to react to market changes and develop and test business strategies without physical risk … or impact to current operations,” Powrie says.
One barrier to implementation, however, Powrie says, has been lack of leadership and stakeholder buy-in. Some C-suite executives don’t trust the scenario from a cost-reduction standpoint, claiming that it doesn’t account for current conditions, he says.
Implementation and Transformation
Supply chain network design isn’t one solution; instead, it’s a combination of people, processes, and technology, Powrie says. “For success in this transformation, cultural alignment and buy-in across the end-to-end supply chain, both internally and externally, are essential ingredients,” he says. Supply chain partners, including third-party providers and suppliers, must be part of the equation, he says: “You have to create that joint benefit.”
Only after the stakeholders have agreed to the business requirements and objectives can a team begin to “build out the true benefit of the digital replica of the supply chain and move on to how to optimize based on what the scenario planning is telling them,” Powrie says.
Another layer to supply chain design is testing the feasibility of the model’s recommendations through simulation: “How can we identify the bottlenecks and reduce the risks associated with that change to the network or footprint.”
Future Capabilities
Artificial intelligence (AI) can be instrumental in building out models associated with creating a digital twin: It can be used instead of manual cleaning when it comes to raw data, freeing up talent to run the scenarios, Powrie says.
Additionally, it’s essential to have “always-on connectivity” that creates real-time track-and-trace capability that supply chain digital twins are going to be demanding, he says. Thus, Internet of Things (IoT) capabilities are critical. For example, if a company’s warehouse is depleted, it should consider such factors as the location of its containers, the inventory they carry, lead times and adjustments based on inventory on hand, he says.
“By combining data from both humans and machines with advanced analytics and predictive insights, we can optimize decision-making in a near real-time manner,” Powrie says. “I feel this the is future of this umbrella of providing enterprises’ the ability for end-to-end transparency — visibility across the supply chain at any moment and into critical aspects of performance. (Companies will realize) a host of benefits from having that real-time visibility into their network, and complementing it by allowing systems to identify alternative scenarios that they can use in decision-making and adjusting to the market.”