Robotics and Outdated Safety Protocols Can Put Warehouse Workers in Harm’s Way
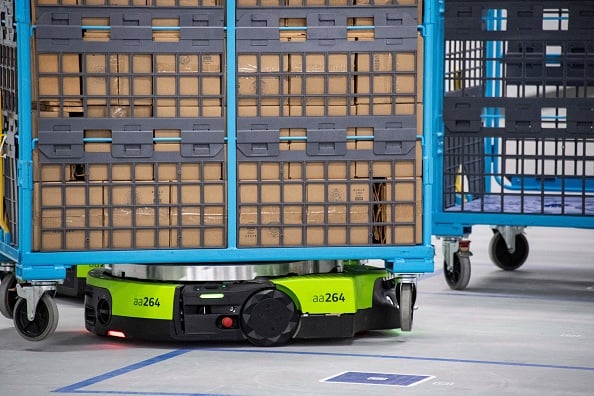
Labor shortages and supply chain disruptions have warehouse workers wrought with exhaustion — physically, mentally and emotionally.
A 2022 industrial-workers report by Philadelphia-based StrongArm Technologies, a safety device and data company, noted that nearly half of survey participants experienced stress on the job and received less than five days of training. Consider this same compromised workforce with outdated safety protocols in place and the integration of robotics on the factory floor, paving a road to harm’s way.
“Whenever a manufacturer or distributor adds new machinery to its facility, it’s a good idea to revisit the on-site safety requirements and guidelines to ensure they are sufficient and identify any gaps,” says Michael Higa, safety advisor for Tempe, Arizona-based Safety Services Company, a safety training and compliance materials business.
Safety Is a Priority
Although the U.S. Occupational Safety and Health Administration (OSHA) currently does not have health and safety guidelines specific to robotics, it does defer to machinery and machine guarding standards, general environmental controls, electrical safe practices, and lockout-tagout (LOTO) — all there to protect the worker, he says.
“A robot is a machine. It does what it is programmed to do. Human beings … not always,” Higa says. Statistically speaking, robotic-based production is a game-changer in injury prevention.
The machine versus human injury incidence comparison is significant. The U.S. Bureau of Labor Statistics stated human private industry workers recorded injury cases of 2.7 incidents per 100 full-time employees. According to OSHA, in the last 40 years, there were 45 reported injury cases involving robot/robotic systems, 32 of which caused fatalities (71 percent). In the past five years, of the 11 incidents involving robots/robotic systems, four were fatal and most involved human error.
The root cause, Higa states, was “not following processes, bypassing barriers or lockout- tagout infractions. If employees followed these safety protocols, many of these incidents could have been avoided, he says.
Safety as a facility priority is paramount to remaining OSHA-compliant, mitigating safety risks of employees and contractors. Higa says, safety programs help prevent or avert workplace injuries while maintaining production.
Today, robotics manufacturers offer better product safeguards. These include, he says, “sensors that stop a robot in motion when an employee is close. Once the employee has moved out of its zone, the robot will start up again.” Collaborative robots, designed for direct interaction with humans, Higa explains, are ideal for a more conjoined workspace, allowing the robot to work at a much slower rate, thus reducing the potential for employee injury.
However, safety issues, while rare, can still occur, raising questions of responsibility. What of the day-to-day docking process when a third-party contract distribution representative parks a truck and waits for the manufacturer or supplier to load product for transport? If the contractor does not know of or follow on-site safety guidelines in relation to a robotic forklift, for example, and an injury occurs, where does the fault lie — on the manufacturer, the robotic manufacturer or the third-party?
Enjuris, a U.S. workers’ compensation platform, states that if a third party negligently caused the injury, a third-party workplace injury claim can be filed, as long as: (1) a third party owed a duty of care, a responsibility to avoid causing harm through their action or failure to act, and (2) the third party breached their duty of care, by not acting reasonably to prevent a foreseeable (anticipated) injury.
The Importance of Training
As with any product or service, maximum efficiency is achieved when used in the correct application. Safety happens, consistently, through training and ongoing implementation. While robotics come with a backbone of reliability, in productivity and sensory engagement, those lines of distinction blur with human interface and frailties therein.
Just as human error is a leading precursor to workplace injury, human safety is achieved through training. According to U.S. National Institute for Occupational Health and Safety (NIOSH) recommendations, says Higa, programmers, operators and maintenance employees need to be trained on a company’s robotic system. Higher safety levels are supported by knowledge of (1) the hazards associated with robotics, (2) the robots’ full range of motion and safety barriers, (3) programming and (4) emergency shut-off details.
As some manufacturing returns to the U.S., more companies will look to automation and robotics integration. In addition to working multiple shifts, “robots do not need breaks. They don’t call out sick, take vacations or get injured,” notes Higa, adding that they don’t make mistakes.
However, human error will always be present, which is why documented training, proper supervision of employees, inspections, observations and retraining are essential when new robotic equipment and corresponding revised procedures are introduced.