The Monthly Metric: Inventory Accuracy Rate
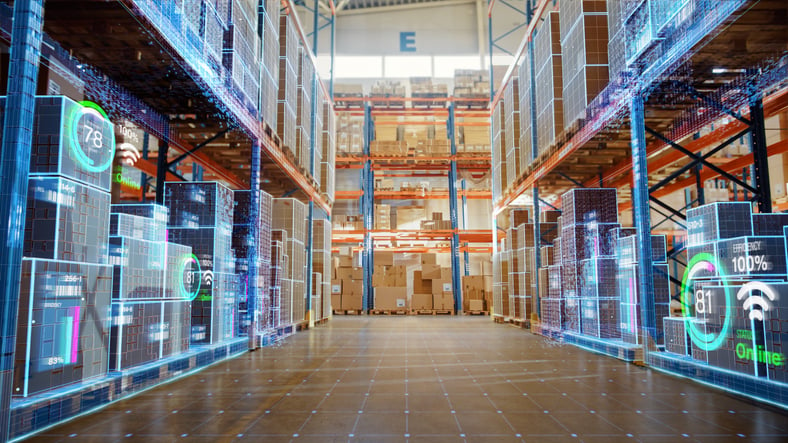
During the coronavirus pandemic, no facet of supply management was likely impacted more than inventories, one of the most critical barometers of the health of a business.
After spending much of the COVID-19 era building healthy buffers to avoid stockouts and ensure supply for customers, many companies are in the process of right-sizing inventories to pre-pandemic levels and returning to just in time (JIT) principles. Such an endeavor makes this month’s metric, inventory accuracy rate, especially critical.
Even in the best of times, inventory accuracy rate has been a demanding scorecard. The measurement goes far beyond how much is on store or warehouse shelves, and “good” benchmark performance is modest compared to other metrics.
The rate covers four phases — planning, ordering, stock keeping and fulfillment — and can be impacted (for good and ill) by stakeholders, says Jim Fleming, CPSM, CPSD, Manager, Product Development and Innovation at Institute for Supply Management® (ISM®).
“It creates an ongoing challenge,” he says. “Inventories and warehouses used to be a secondary focus for supply managers who are now being asked to be on top of the planning, production and delivery phases. An end-to-end supply chain brings those dynamics more to the forefront, requiring a lot more strategic thinking.”
Inventory accuracy rate highlights the suite of measurements in The Metrics of Inventory Management, released in 2023 by CAPS Research, the Tempe, Arizona-based organization in strategic partnership with ISM and Arizona State University. The report of KPIs and benchmark data for the inventory and warehouse management functions is modeled after The Metrics of Supply Management, CAPS Research’s flagship report.
Meaning of the Metric
Inventory accuracy rate is calculated via a simple fraction, the number of counted product stock-keeping units (SKUs) divided by the number of units on record. An accurate count — performed by a human count or with a warehouse management system (WMS) — of what’s in stock helps avoid inventory shrinkage. It also eases operations and accounting processes and improves supply chain visibility.
This makes multiple functions in a company happy, which can be ironic: Accuracy is complicated, Fleming says, in that ideal inventory levels vary between stakeholders.
“The sales organization is usually confident it will sell and so errs on the side of having more inventory. Operations people generally want some buffer,” Fleming says. “If you talk to finance, they’ll say inventory costs a lot of money, so keep it as low as you can. So, you get mixed signals.”
In walking this tightrope, inventory managers have not been able to rely on technology as a balancing pole. As a result, benchmarks are lower than for many other metrics: The CAPS Research report indicated an average of 91 percent, with the lowest-performing companies at 67 percent. Other studies have found average inventory accuracy rates as low as 65 percent.
“Given that there are so many variables to manage, 90 percent is good,” Fleming says. “And I would consider 95 percent world class.”
Technology is Catching Up
Manual tracking — with most advisers recommending cycle counting of small portions of inventory until the entire stock is accounted for — will always be a part of accuracy rate calculation. But keeping up with the many moving parts in an end-to-end supply chain requires the help of technology.
The Metrics of Inventory Management found that the technologies most used to manage inventory accuracy are (1) ERP and accounting software, (2) barcode scanners and (3) WMS. For the stock-keeping phase, 100 percent of respondents said their companies use a WMS.
However, Fleming says, such technology implementation remains nascent, as the “out of sight, out of mind” concept can apply to logistics and warehouse management during a company’s budgeting process.
“Warehousing and logistics are generally at the end of the spectrum in a company when it spends money on systems and technology,” he says. “Those managers have to fight for whatever they can get. So, while the data says technology helps make inventory management more sophisticated versus physical counting, many companies are still working toward integrating full solutions.”
Artificial intelligence (AI) is playing a growing role. An AI-based camera system can count inventory as it comes off a truck, and drones can fly through warehouses, photographing inventory on pallets or shelves and comparing to SKU levels reported in the WMS.
Technology is a high priority for third-party logistics (3PL) providers, and many companies — including Intel Corp, where Fleming served as a capital-equipment supply chain manager from 2007-14 — have outsourced warehousing and inventory operations, with improved accuracy rate among the benefits.
“That’s one of the core competitive advantages (of a 3PL),” Fleming says. “They’re investing in technology and willing to put money forward to make it a more sophisticated warehouse. At Intel, we owned all of the warehousing for years and we finally realized that wasn’t a competitive advantage. But many third-party companies have that level of sophistication.”
A ‘Pendulum Shift’ Back to JIT
Many factors play into inventory levels — particularly demand, which has been sluggish amid economic uncertainty. The Manufacturing ISM® Report On Business® Inventories Index has been in contraction territory for 13 straight months. In the services sector, especially in health care, executives and supply managers have expressed sentiment on right-sizing their inventories to more in line with levels before COVID-19.
The pandemic started a great inventory-model debate: JIT vs. a just-in-case (JIC) philosophy of higher levels to mitigate the risk of stockouts. Though the final buzzer has not yet sounded, it appears JIT has won the game yet again, as it did through the 2008 global financial collapse and such rising threats as climate change and geopolitical turbulence.
Fleming envisions what he calls a “more sophisticated” JIT. “It has to be more sophisticated to accommodate the higher degree of variability, and technology is able to provide the information and insights to make it work,” he says.
Through it all, accuracy remains most critical. “The pendulum won’t shift all the way back because procurement teams remember the trauma of the pandemic and don’t want to run out of inventory again,” Fleming says. “Business is always going to be cyclical, but being on top of demand and inventory will make those ups and downs more manageable.”
To suggest a metric to be covered, email me at dzeiger@ismworld.org.