The Monthly Metric: Trailer Utilization Rate
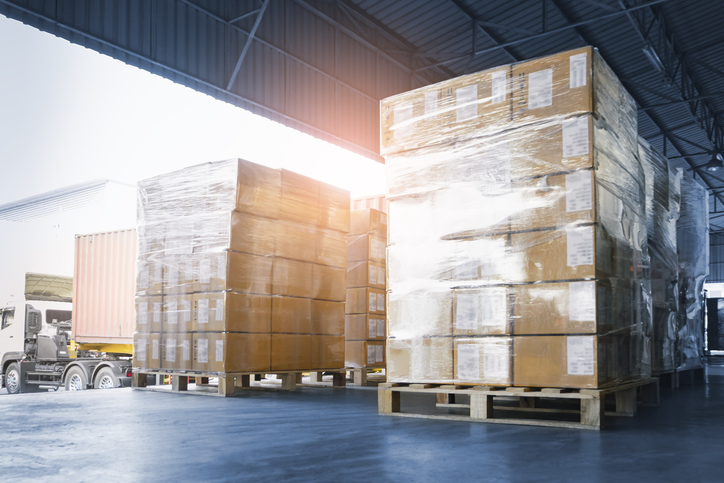
The analytic featured in this edition of The Monthly Metric — the focus of a report last year by the U.S. Postal Service’s (USPS) Office of Inspector General (OIG) — is one supply managers should be cognizant of amid a continuing trucking recession.
Trailer utilization rate has traditionally been a challenging metric to master for trucking companies. It can be a dichotomy: Every inch of unused space is a lost opportunity for revenue, but an excess of trucking capacity due to fleets of trailers that are only partially full or idle contributes to depressed freight rates.
Under such conditions, maximizing trailer utilization is critical, as it helps limit fuel costs, improve the bang for driver compensation bucks, and avoid unnecessary fleet wear and tear. That’s not only in the interest of trucking companies, but also procurement organizations that need products shipped.
“Trucking companies don’t realize how badly they underutilize their trailers,” Francis Roy, then-vice president of vHub, a Canada-based trailer utilization platform, told FreightWaves in 2020. “That speaks to the need of our carriers to understand what is going on with their fleets to utilize their assets.”
Meaning of the Metric
Trailer utilization rate is a self-defining analytic, indicating the percentage of trailer space occupied on a delivery. Roy told FreightWaves that even “the best in the game” utilize no more than 80 percent of their trailer space.
Last year, 43 percent of truckloads moved at less than full capacity, according to Wasted Space, Wasted Dollars: The Economic Impact of Inefficient Freight, a report by Flock Freight, an Encinitas, California-based shipping data and technology provider, and Drive Research of Salina, New York.
Such inefficiencies add to price pain in a business that has become more expensive than ever — the average per-mile operational trucking cost exceeded US$2 for the first time in 2023, according to the American Transportation Research Institute (ATRI), the research arm of American Trucking Associations — higher prices for fuel, repair and maintenance, and driver pay get passed on to procurement organizations.
Shipping timelines are also impacted: Flock Freight found that, when faced with a partially empty load, shippers have two alternative choices: (1) rely on a more expensive and unpredictable less-than-truckload (LTL) carrier or (2) wait to ship until a truck can be filled. The report noted that 16 percent of shippers booked truckloads “often” or “very often,” sacrificing cost efficiency but avoiding another option that might not deliver the freight on time.
“Historically, the U.S. truckload market has been locked into a binary concept of ‘full’ or ‘empty’ when it comes to trailer capacity,” Flock Freight COO Chris Pickett said in a press release. “We are challenging both shippers and carriers alike to rethink this.”
Case Study: The U.S. Postal Service
Of 441 USPS facilities tracked in fiscal year 2022, 86 had a trailer utilization rate of 66 percent or better, 272 were between 40 percent and 65 percent, and 81 failed to hit the USPS goal of 40 percent, according to the OIG.
“While the (USPS) has increased its emphasis and developed initiatives to address underutilized transportation,” the report stated, “trips were still being underutilized because local transportation management did not consistently monitor and adjust transportation schedules.”
The report added that, in many cases, trailer utilization space was inaccurate because a load scan — an automated process in which laser scanning technology measures the volume of material in a trailer — was not performed.
For the USPS and other carriers, inefficient space utilization or idle trailers can come at a cost. An OIG audit in 2020 found that the USPS spent $7.1 million on idle trailers during a 14-month period.
The OIG made two recommendations: Eliminate or consolidate shipments with less than 40 percent utilization at some facilities, and improve the load scan rate, which was 85.8 percent, the report found. USPS officials agreed with the latter recommendation but balked at the former, leaving the OIG to consider the matter unresolved.
Regarding shipment elimination or consolidation, the OIG report states: “(W)hile we recognize that the (USPS) has processes in place, we found trips remain underutilized and we identified redundant and empty trips where there was opportunity for local management to consolidate or eliminate.” The OIG will pursue the matter “through the audit resolution process,” the report states.
Upping the Utilization Rate
A sizeable pool of trailers is important for carriers’ flexibility, but utilization rates can improve when there is less potential capacity. ATRI found that the average number of trailers per truck was 2.71 in 2022, down from 2.9 in 2020.
While a 100-percent utilization rate is not possible or even ideal, Roy told FreightWaves, fleet management technologies are becoming more prevalent. Cargo sensors and route optimization software help carriers detect empty space, better match vehicles to routes and maximize daily deliveries.
Finally, one of the most vital assets is communication and collaboration, wrote Grant Stinson, national account manager at Global Tank, an Overland Park, Kansas-based company specializing in liquid and dry bulk tank trailer sales and rentals.
“Fleet managers need to work closely with internal stakeholders, including procurement teams, logistics personnel and customers, to align objectives and ensure smooth operations,” Stinson wrote on LinkedIn. “Furthermore, fostering strong relationships with external partners, such as carriers, shippers and third-party logistics providers, enhances coordination and facilitates effective supply chain execution.”
A trucking freight calvary is not coming, at least for the rest of this year. Therefore, carriers and procurement organizations will have to improve efficiencies to maximize trailer utilization and get through the trucking recession.
To suggest a metric to be covered, email me at dzeiger@ismworld.org.