The Monthly Metric: Total Manufacturing Cost
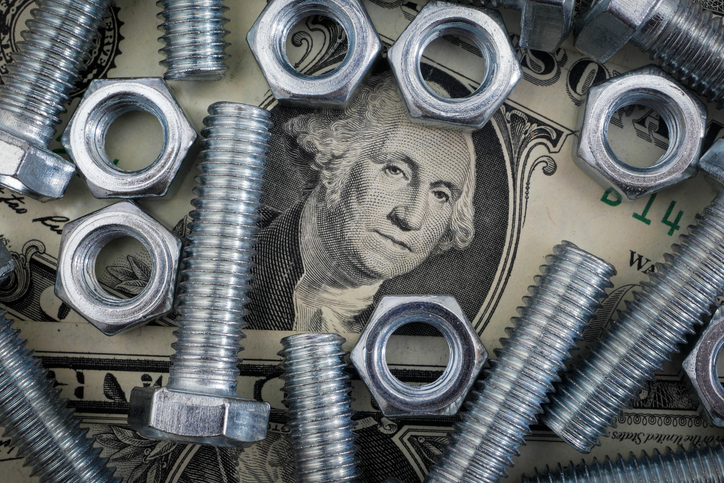
Supply management professionals’ responsibilities have moved well beyond buying materials to raising efficiencies and improving performance from sourcing to end-user delivery, and this month’s metric reflects that evolution.
While total manufacturing cost (TMC) is a good barometer of success at multiple stages of the supply chain universe, its use is hardly universal. Companies track the elements of the analytic, but not all of them view the entire picture, says Jim Fleming, CPSM, CPSD, who is Manager, Product Development and Innovation at Institute for Supply Management® (ISM®).
However, he says, that could be changing amid the growing strategic focus on the end-to-end supply chain.
“We’re thinking more about all of the dynamics that fit into cost,” Fleming says. “We were traditionally focused on cost reduction of a widget or direct material, but in the full ecosystem, there has been a lot of factors that supply managers have not engaged in. But we’re becoming much more in tune to it.”
A greater understanding of TMC — which includes inventory (at all three stages; more on that later), labor and overhead expenses — can help a supply manager better determine when and how much material to buy, mitigate spoilage risk and identify potential inefficiencies in the production process.
Improved TMC performance can enhance the use of other metrics like TCO and cost of goods sold (COGS). And it can reduce waste and aid in pricing strategies.
Fleming uses an analogy of a car engine: “When you really understand TCO, you look at it with an understanding of the costs in logistics, transportation and warehousing. That’s a big part of the equation,” he says.
“Another is the cost of manufacturing, including how materials are used and stored. So, as we learn more about cost though these parts of the engine, we’re refining and identifying the parts that can help us improve overall performance.”
Meaning of the Metric
Total manufacturing cost is what a company pays to have a product produced — direct materials and labor, plus overhead expenses like facility rent and maintenance, energy bills and indirect materials or labor. Such expense tracking, especially for the various stages of inventory, can be uncharted territory for many supply mangers, Fleming says.
“Until recently, that was considered a whole new level of granularity,” he says. “Thinking about the inventory you’ve bought in, the inventory in process, as well as labor and overhead to deal with it … can lead to a lot of deer-in-the-headlights looks.”
He continues, “Employees think, ‘You want me to understand how much inventory is used by manufacturing in a given day, and how to optimize it for sales and operations planning? I’ve just been responsible for getting it here.’ As procurement gets more integrated into functions like finance and operations, they’re starting to peel back that onion.”
A better grasp of TMC is perhaps most valuable in inventory management, Fleming says. As this space has documented often, inventories are one of the most challenging supply chain dynamics, even in the best of times and especially during the coronavirus pandemic.
Increased visibility into the cost impact of not only raw materials inventory, but also work-in-process and finished goods, can help procurement professionals gauge demand and order more strategically — which can lead to better balance between controlling inventory costs and avoiding stockouts. A similar approach can be taken with labor and overhead.
“Some of the leading organizations have better tools and indicators that bring that level of awareness for everybody into the stakeholders, where they can dig down into the cost per unit,” Fleming says. “Then, as you start seeing all the data, you’re getting educated around how your area fits it — and how you might be able to influence it. That’s when things really click.”
Opinions vary on whether unused or spoilage materials should be included in the TMC equation. Since the money has been spent, Fleming says, such materials should be included: “You invested the cash to get it, so you need to track how efficiently you’re reaping the benefit,” he says. “A good example is something I lived through in semiconductor manufacturing.”
A Case Study Involving Chemicals
Fleming, a capital-equipment supply chain manager at Intel Corporation from 2007-14, faced an TMC issue involving chemicals used in the semiconductor wafer production process. The supplier indicated the chemicals had a two-year shelf life, but to mitigate safety risk, Intel cut that in half, disposing unused stock after a year.
To lower TMC, Fleming says, Intel tested the chemicals and found that their shelf life did, indeed, approach two years. So, the company began using them for materials with higher technology nodes and lower risk. (In semiconductor production, a lower technology node generally means smaller, higher-density transistors with increased speed and performance.)
“If you have a technology that’s older and the margins are lower, based on how much is being sold, you need to figure out how to cut back manufacturing cost,” he says. “We extended the chemicals for lower-risk products, and it drove down our cost.”
The impact was felt beyond Fleming’s team: “When engineering and R&D knows that (extending chemical shelf life) is an option,” he says, “it impacts some of their decisions, and that could further improve efficiencies.”
TMC is a metric, Fleming says, that fits in with systems thinking — holistically analyzing a dynamic (cost) and identifying how a component or factor (like inventory or chemical shelf life) impacts the whole. When a component of the system is optimized, the entire operation benefits. In the age of end-to-end supply chains, TMC will become even more critical.
“It’s an indicator that may not be in the forefront at a lot of companies,” Fleming says, “but it’s going more relevant at some point in the near future.”
To suggest a metric to be covered, email me at dzeiger@ismworld.org.