Sound Supply Chain Decisions Boost Bottom Lines
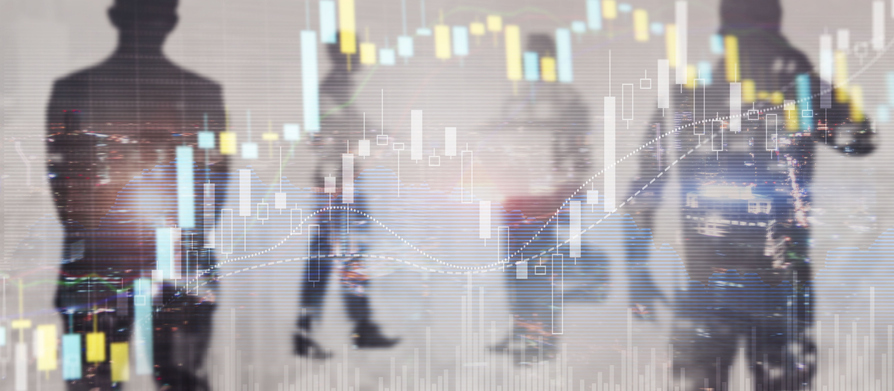
The modern business environment, characterized by a globalized market and heightened competition, necessitates efficiencies at every operations level — and supply management stands out as a critical driver of profitability and overall financial performance.
The network of sourcing raw materials, manufacturing, transportation and distribution to the final consumer determines operational efficiency and significantly influences a company's profitability.
There is an intricate relationship between supply chain decisions and corporate profitability, underpinning the connection with financial ratios and real-world examples.
Understanding Supply Management
At its core, supply management encompasses the processes involved in producing and delivering goods or services, from sourcing raw materials to reaching the end consumer. Effective supply management, no matter the industry or sector, aims to streamline these processes, reduce costs and improve service delivery.
For manufacturing companies, supply chain decisions related to raw material procurement, production scheduling, inventory management and distribution are critical. Efficient management can lead to lower production costs, reduced lead times and increased throughput, thereby improving the bottom line.
At retail businesses, supply chain decisions influence inventory levels, product availability and store operations, necessitating a balance between carrying costs with stockouts and markdowns. Accurate demand forecasting and efficient inventory management can significantly impact profit margins.
Technology companies, particularly those in hardware, benefit from supply chain efficiencies by reducing component cost, shortening time to market, and enabling rapid scaling of production to meet demand. Dell’s direct-to-customer model is a prime example.
Even service providers, which may not deal with physical goods, rely on efficient supply management processes and workflows to deliver services, leading to cost savings, improved service quality and enhanced profitability.
No matter the type of business, industry sector or scale, supply chain decisions dictate a company’s financial health. This universal truth underscores the significance of strategic, well-informed supply management, positioning it as an essential element in any successful business model.
Profitability
Supply chain managers make decisions that directly impact a company’s financial performance. Creating awareness of the connections between supply chain decisions and financial performance enables managers to make informed decisions, thus understanding the impact of a thorough and meticulous decision versus an isolated one.
Financial items impacted by supply management include income statement and balance sheet items.
Income statement items to consider:
- Revenues. A well-orchestrated supply chain ensures timely and accurate delivery of products or services, enhancing customer satisfaction and loyalty. An agile supply chain can quickly adapt to market changes or customer demands, capturing sales opportunities and driving revenue growth.
- Cost of goods sold (COGS). Effective sourcing strategies, streamlined production processes and optimized logistics reduce COGS and improve gross profit margins. For instance, negotiating better terms with suppliers or implementing lean manufacturing can significantly lower production costs.
Customer service levels also have a direct impact on finances, as poor service can lead to lost sales, while high service levels can boost repeat business. Efficient logistics planning can reduce transportation and warehousing costs, whereas poor planning may lead to higher expenses due to expedited shipments.
Inventory management plays a crucial role; excess inventory ties up cash and incurs carrying costs, while insufficient inventory can result in stockouts and lost sales. Effective inventory management helps strike the right balance. Labor costs can escalate quickly with unplanned expenses such as overtime or additional shifts, but optimizing workforce planning can mitigate these costs.
Additionally, material costs are influenced by supplier contracts and purchasing strategies. Poor contracts or scattered volume across multiple suppliers can increase costs, whereas consolidating purchases and negotiating better terms can lead to significant savings.
Balance sheet items to consider:
- Inventory levels. Higher inventory levels tie up cash and increase carrying costs, while efficient inventory management reduces these burdens.
- Accounts receivable. Improved customer service can lead to faster collections and lower accounts receivable.
- Accounts payable. Favorable payment terms with suppliers can improve accounts payable, enhancing cash flow.
Financial Ratios
Additionally, understanding how supply management impacts financial ratios can enable companies to make more informed decisions that drive profitability.
Activity ratios to consider include (1) days of inventory on hand (DOH) — efficient inventory management reduces DOH, indicating better inventory turnover and less cash tied up in stock — and (2) days of sales outstanding (DSO), as faster cash collection from customers improves liquidity and reduces DSO. Also, look at number of days payable: Favorable payment terms with suppliers can extend the number of days payable, improving cash flow.
Liquidity and profitability ratios to look at:
- Cash conversion cycle (CCC), which indicates the time it takes for a company to convert investments in inventory and other resources into cash flows from sales. A shorter CCC means better liquidity and less need for external financing.
- Gross profit margin. Lowering COGS through efficient supply chain management boosts gross profit margin, indicating higher profitability.
- Return on assets (ROA). A well-managed supply chain ensures that assets, like machinery, warehouses or vehicles, are utilized optimally. Optimized asset utilization, driven by effective supply management, improves ROA by generating higher returns on the company's assets.
By understanding and optimizing the impact of supply chain decisions on financial metrics, companies can achieve greater efficiency and profitability. Aligning supply management with financial goals ensures that businesses remain competitive and profitable in a challenging market. Companies that neglect this vital aspect of their operations may find themselves at a competitive disadvantage, struggling to maintain profitability and market share.