The Monthly Metric: Unscheduled Downtime
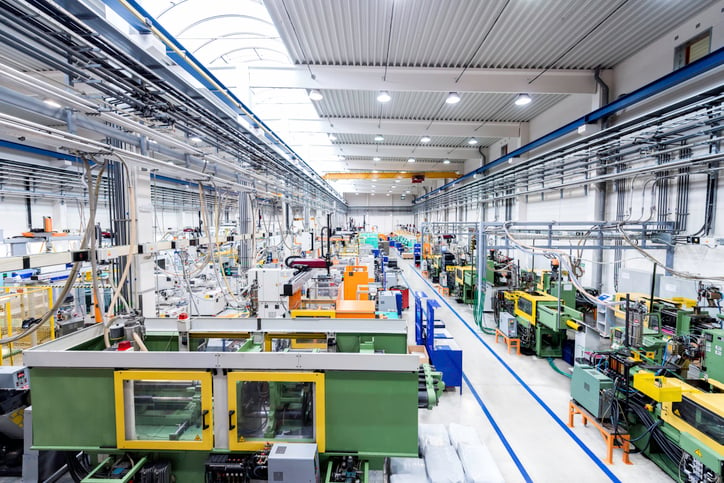
When a factory is not running, a company is usually losing money, and electric vehicle manufacturer Tesla provides a high-profile case study on the cost of manufacturing downtime.
In March, a suspected arson attack at a German plant resulted in a week-long power loss, halting production and costing Tesla more than 100 million euros (US $111.6 million). It was another disruption headache for the company, which in recent years has planned (due to facility upgrades) and unplanned (a COVID-19 outbreak in Shanghai) downtime that led to lower-than-expected deliveries and cautious investors.
“Money furnaces,” was how Tesla CEO Elon Musk described the idle facilities in a 2022 quarterly earnings call.
As a General Mills spokesperson stated, “It’s common for manufacturing plants to incur downtime. We try to anchor that to holidays when we’re able, to minimize any disruption.” When downtime is unscheduled due to unexpected circumstances like equipment failures, system outages or product shortages, it becomes especially costly. Multiple studies indicate that it’s getting more expensive every year — even amid fewer hours in downtime, on average.
The True Cost of Downtime 2024 report by German technology company Siemens found that unscheduled downtime saps 11 percent of annual revenues from the world’s 500 biggest companies — a total of $1.4 trillion, an increase from $864 billion (8 percent of revenues) in 2019 and ’20. In the automotive industry, the per-hour cost is $2.3 million, or $600 a second.
Last year, in its Value of Reliability report, Swiss electrical equipment manufacturer ABB found that among the more than 3,200 global plant maintenance leaders surveyed, two-thirds of companies dealt with unplanned downtime at least once a month, at a cost of $125,000 an hour.
“The high cost of downtime increasingly constrains industrial businesses in an already uncertain landscape. This encompasses both direct costs like wasted production or spare parts, and indirect costs like reputation and morale,” Virve Viitanen, head of global customer care and support at ABB’s motion services division, wrote in the report.
The costs and consequences of unscheduled downtime impact an entire supply chain, making it a critical measurement to track.
Meaning of the Metric
The ISM Glossary of Key Supply Management Terms defines downtime as the “unproductive time when manufacturing processes are stopped and workers are idle, usually as the result of equipment failure, setup, maintenance work or material shortages. Also applicable to services when service delivery is interrupted as a result of failure of equipment or people in the service delivery process.”
Unscheduled downtime can be calculated by logging the duration of each shutdown that falls outside of planned maintenance/upgrades and scheduled breaks. Measured on a monthly basis, for example, it can be calculated as a percentage of expected production time. A higher percentage indicates a need for improved preventive maintenance or equipment reliability.
Perhaps the biggest reason unplanned downtime has become so expensive for companies: Its costs, especially for resulting supply chain disruptions, have outpaced inflation. There are also hidden costs, Siemens researchers note, including paying for (1) employees unable to work, (2) emergency replacement parts at a premium and (3) penalties for failure to meet contractual obligations.
“Goods cost more, so the value of those not made during downtime is greater,” Jim Davison, national membership director at Make UK, a London-based manufacturing advocacy organization, said in a Siemens press release. “(W)ith many factories operating at higher capacity, there is less slack in the system to make up for lost time. The higher cost of energy, labor and materials wasted when production lines fail also contributed to a perfect storm of costly downtime challenges for major manufacturers.”
This dynamic can be exacerbated at smaller businesses and suppliers, which are more vulnerable to financial strain and inventory stockouts. Especially for smaller organizations, ABB researchers note, a downtime audit is a critical first step: understanding direct and indirect costs, the equipment most impacted and the wider business implications.
Downtime Reductions: What’s Working
Amid the increasing costs of downtime, the irony is that Siemens researchers found that most companies have reduced their unscheduled downtime hours — the only reason expenses “have not spun out of control,” The True Cost of Downtime 2024 states.
On average, major manufacturers experience 25 downtime incidents a month, compared to 42 in 2019. The average of 27 lost hours monthly is down from 39 five years ago. However, a plant typically takes longer to resume operations following a shutdown.
Predictive maintenance, which uses artificial intelligence (AI) to analyze data on factory machine health — including overall equipment effectiveness — to forecast equipment failures and schedule maintenance, is called a “must-have” technology by Siemens. “Fixing before failure reduces the need for replacement parts by up to 40 percent, reducing wastage and carbon usage,” the report says.
Other strategies include training staff to conduct effective troubleshooting and minimize downtime during emergencies, as well as keeping critical spare parts readily available. 3-D printing, which can create a replacement part on-site, has been identified as a downtime saver.
“An hour of downtime costs significantly more than it did two years ago. This is a drag on profits that businesses can no longer afford to ignore,” Robert Russell, head of predictive maintenance strategy and delivery at Siemens, said in a press release. “However, digitization and predictive maintenance efforts are starting to have a significant impact, and most manufacturers have successfully reduced the number of incidents affecting production.”
Pauses in production, whether expected or not, are a fact of life for companies and their manufacturing operations. However, advanced technologies and proactive mitigation strategies can limit unscheduled downtime, increase operational efficiency — and reduce the flames from a money furnace.
To suggest a metric to be covered, email me at dzeiger@ismworld.org.