The Monthly Metric: Available-to-Promise Inventory
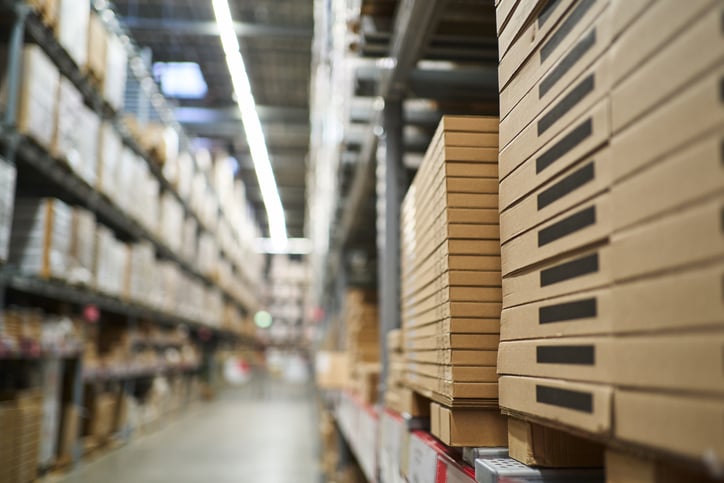
Since the start of the coronavirus pandemic, perhaps no element of supply management has commanded the attention of practitioners more than inventories.
For most companies, keeping as little money as possible tied up in inventory while avoiding stockouts is a tightrope, even in the best of times. COVID-19 brought unprecedented supply chain disruptions and consumer demand swings that made inventory management a vexing puzzle to solve.
As a result, inventory performance metrics and KPIs have been frequently discussed in this space during the last four years. And as The Monthly Metric approaches the end of its life cycle — more on that next month — it’s fitting that trend continues.
That dead or obsolete stock can make up as much as 30 percent of a company’s inventory illustrates the challenge. Such stock is expensive, and the reputational hit if customers are left waiting can be just as or even more costly. A metric that can be a make-or-break indicator of ability to deliver on customer expectations is available-to-promise (ATP) inventory.
“It is not enough to just present a quantity; demanding shoppers also want to see an expected date of delivery — not an estimated date of when a product will be shipped, but a precise date of delivery at their doorstep or a confirmed date for in-store pickup,” Sudhir Balebail, product management leader, order management at IBM, wrote last year. “This means keeping track of stock availability, capacity availability and, possibly, the availability of specific delivery slots for pickup.”
Meaning of the Metric
ATP inventory provides a snapshot of the quantity of products available for sale or shipment without impacting existing customer orders. It indicates the amount of inventory that a company can confidently “promise” to deliver to new customers by a specified date while honoring commitments already made.
The metric is particularly critical in industries with high levels of demand fluctuation or seasonality, like retail, manufacturing and e-commerce. For example, a retailer can rely on ATP to understand how much stock is truly available for end-of-year holiday orders. Such data can better inform supply managers of their company’s safety-stock levels, and when to reorder.
When measured effectively, ATP inventory can help companies find an ideal hybrid — long sought in the COVID-19 era — between tried-and-true just-in-time inventory and a prudent amount of buffer stock for unexpected demand or shortages, without overextending resources or disappointing customers.
The calculation can vary slightly, depending on the specifics of the business and the level of detail required. Typically, ATP inventory is determined in two ways: discrete (measured on a weekly or monthly basis) and cumulative (a longer-term view).
Discrete — or incremental ATP, for goods that will sell or expire before the next weekly or monthly measurement period — is calculated by adding the stock on hand and incoming inventory, then subtracting committed customer orders.
As an example, a company has 500 widgets remaining in stock this month, and it produces 1,200 widgets every month. It signed a contract to provide 1,000 widgets to a retailer by the end of the month.
The calculation: (500 + 1,200) - 1,000 = 700. The company has 700 widgets available for all other orders.
This approach gives businesses a clear view of how much inventory it can promise customers within each period. However, if one period has excess inventory while another has a shortage, the discrete ATP method will not necessarily account for this unless replenishment is scheduled accordingly.
The cumulative ATP method factors all scheduled production or procurement across future periods. The formula takes the previous ATP balance and adds incoming inventory, then subtracts committed orders.
In this method, ATP balances are carried over from one period to the next, creating a cumulative view. This allows companies to better handle fluctuations in demand by reallocating surplus inventory from one period to a shortage in another.
For example, a company with an unexpectedly high ATP balance in January can use that surplus to fulfill February’s anticipated high demand. “The main advantage to this ATP calculation,” states a 2023 Microsoft Learn article, “is that it can handle instances when the sum of issues between receipts is bigger than the latest receipt, for example, when it is necessary to use a quantity from an earlier receipt to meet a requirement.”
How ATP Benefits Entire Supply Chains
ATP influences decision-making across functions. It’s essential for demand planners who aim to match supply with projected demand. By keeping a close eye on ATP levels, planners can ensure they’re well-prepared for future customer orders, adjusting as necessary to match changing demand patterns.
Armed with accurate stock data, sales and customer service teams can confirm availability and delivery times accurately. This directly impacts customer satisfaction, as companies avoid taking orders they cannot fulfill within a promised timeframe.
By knowing exactly how much inventory is available, companies can make data-driven decisions about when to ramp up production or when to pause, helping to minimize both excess inventory and stockouts. Marketing teams can adjust promotional campaigns and special offers to align with available inventory, reducing the risk of promising products that can’t be delivered.
As a result, improving ATP performance can lead to strategic adjustments to streamline a supply chain. Here are a few tips for companies looking to optimize their ATP performance:
Enhance real-time data visibility. By investing in systems that offer up-to-date visibility into on-hand inventory, scheduled incoming inventory and customer orders, companies can make ATP decisions quickly and accurately. Advanced technologies like the Internet of Things and RFID can offer further enhancements by tracking inventory movement across locations.
Improve demand planning. Demand planning tools that leverage predictive analytics and machine learning can help companies anticipate demand fluctuations and adjust ATP calculations proactively.
Set safety stock levels and lead-time buffers. By establishing safety stock levels to absorb demand fluctuations and lead-time buffers, companies can protect their ATP calculations from being impacted by unexpected supply delays.
Use cross-functional collaboration. ATP performance improves with synergy between departments like sales, production, procurement, and customer service. Cross-functional communication protocols enable teams to update ATP in response to such changes as a large incoming order, delay in raw material delivery or shift in production schedules.
ATP is a critical metric that allows companies to balance supply and demand while making strategic decisions about customer order fulfillment. With accurate ATP monitoring, businesses can avoid overpromising or under-delivering, which is key to maintaining strong customer relationships.
With ATP at the center of decision-making, businesses can achieve greater visibility, flexibility, and responsiveness in their supply chain operations.