Revolutionizing Warehouses with ASRS
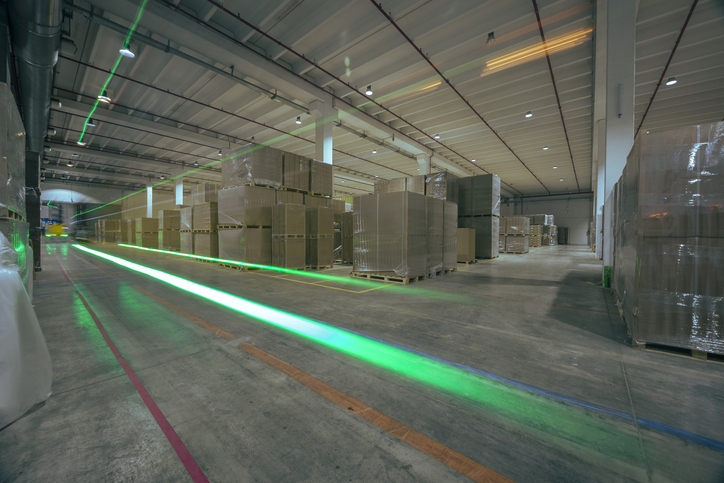
The warehousing and distribution industry is in the midst of a transformation driven by the widespread adoption of automation. By reshaping operations and addressing the industry’s longest standing challenges, solutions like automated storage and retrieval systems (ASRS) are paving the way for a new era of efficiency and precision.
And, as e-commerce trends continue to surge and customer expectations rise, automation is necessary for modern warehouses and distributors to adapt to remain competitive.
The Rapid Rise of Automation
Early on, ASRS were largely confined to large-scale, high-volume operations. Today, however, they are highly versatile and scalable solutions, making them accessible to warehouse and distribution centers (DCs) of all sizes.
Now combined with a network of key technologies, including automated guided vehicles (AGVs) and robotic picking systems, an ASRS utilizes computer-controlled systems to automatically place and remove loads from various storage locations. With the help from AGVs, the goods are transported throughout the warehouse with minimal intervention. Advanced robotic picking systems manage and sort the items with high speed and accuracy — all leading to dramatic improvements in operational efficiency.
Because traditional warehousing relies heavily on manual labor, slow processing times, high error rates and inconsistent quality control are everyday challenges. Fortunately, automated systems address these inefficiencies in several ways:
Increased speed and throughput. In warehouses and DCs, automation significantly increases the speed of operations compared to manual processes. For example, an ASRS can move items rapidly, accelerating order fulfillment and reducing lead times. Having a high-speed warehouse is critical to meet the growing demands of e-commerce and just-in-time (JIT) inventory models.
Enhanced accuracy. Moreover, ASRS minimizes human error, a common problem in manual warehousing. Robotic systems and automated pickers are able to manage items with extreme accuracy, ensuring orders are fulfilled carefully and correctly, reducing wasted inventory and returns caused by shipping errors.
Additionally, most ASRS solutions come with integrated inventory management software that has track and trace capabilities that can track stock levels in real time. This enhances forecast accuracy and reduces stockout risks and overstocking, which both impact profits and customer satisfaction.
Better space optimization. An ASRS often comes with advanced inventory management software to help optimize storage space. High-density storage solutions like vertical lifts and conveyor systems help distributors make the most of the available space, an asset that is especially important in areas where real estate is expensive.
Furthermore, the data collected by automated systems can be analyzed to help identify trends and optimize workflows. For instance, data on pick rates and storage space utilization can help warehouse managers make better decisions on the layout and design of the warehouse or improve processes.
Scalability and flexibility. Automated systems can easily grow or be reconfigured as business needs evolve. Extra storage modules and robotic units can be added to existing operations with little disruption. This level of flexibility lets warehouses and DCs adjust to changes in order volumes and inventory levels without requiring major investments.
Further, automated systems, like ASRS, are designed to handle a large variety of products, from large to small. Automation helps distributors adjust to accommodate several types of inventory, ensuring that warehouses remain agile and responsive at all times.
Addressing Today’s Labor Challenges
It’s no secret that the warehousing and distribution industry frequently struggles with labor shortages and high turnover. Recent data shows that there are about 8.1 million job openings in the U.S., but only 6.8 million unemployed workers — meaning there are more positions than people to fill them.
However, automation plays a key role in helping warehouses and DCs combat labor challenges by reducing the reliance on humans and creating more skilled positions. Additionally, it can help with:
Reducing dependence on humans. Automated systems, including ASRS, manage repetitive and physically demanding tasks like lifting and sorting to ease the burden on human workers. This approach not only helps tackle shortages, but also enhances worker safety by lowering the risk of injuries associated with manual labor.
Attracting and retaining talent. Warehouses that adopt automation can create more attractive work environments for prospective employees. Employees are more inclined to stay in safer positions and automation can open new job opportunities.
The Supply Chain of the Future
Automated storage systems are changing the game for the warehousing and distribution industry by helping to tackle their biggest challenges and inefficiencies.
Thanks to innovative technologies, warehouses are becoming faster, more accurate and much more adaptable. As the industry evolves, these automated systems are likely to become the norm, setting new benchmarks for how warehouses operate.
Adopting these innovations isn’t just about staying on trend — it’s a smart move towards building a more resilient and agile supply chain for the future.